Этиленник «Нижнекамскнефтехима» принял первое сырье
Один из масштабных проектов развития нефтехимической отрасли России вступает в финальную фазу подготовки к официальному вводу в эксплуатацию
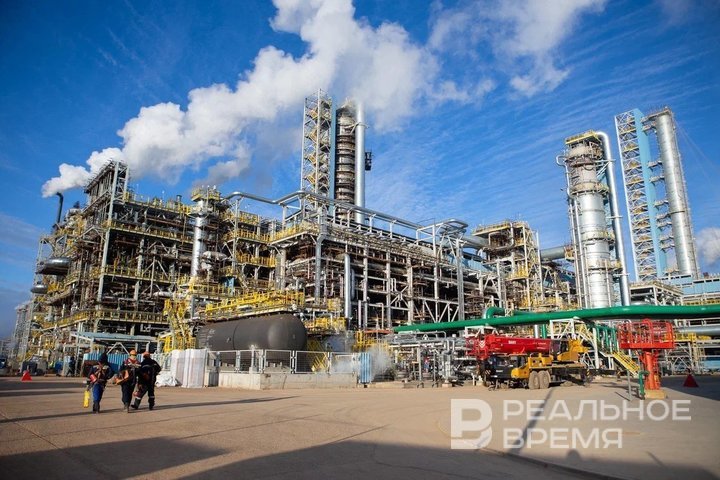
«Начинаем прием сырья на печь №1. Усилить контроль. — Принято». С этих слов началась новая страница в истории олефинового комплекса СИБУРа. В присутствии десятков камер и журналистов на ЭП-600 НКНХ приняли первое сырье. Так стартовал один из наиболее значимых этапов «горячей» пусконаладки этиленника. За ним последуют тонны первой продукции, положительное заключение надзорных органов и постепенный выход на проектную мощность — 600 тысяч тонн этилена в год. О том, как проходила подготовка к запуску и кто вершит историю, — в репортаже «Реального времени».
«Замечаний по технологическому режиму нет»
Значимое историческое событие произошло в Нижнекамске — первое сырье принял новый этиленовый комплекс ЭП-600. Вместе с нефтехимиками радость разделили российские и республиканские журналисты, для которых был организован пресс-тур по строящимся производствам «Нижнекамскнефтехима».

— Начинаем прием сырья на печь №1. Усилить контроль, — уверенно дал команду один из работников комплекса в операторной.
— Принято, — тут же послышалось в рации.
Журналистам рассказали, что на стадии тестирования печи пиролиза будут загружены на 60%. Прием сырья происходит в автоматическом режиме, процесс контролируют аппаратчики из центральной операторной. Для безопасной и комфортной работы в здании есть все необходимое — комната психологической разгрузки с массажными креслами и капсулами для сна, обучающий симулятор-тренажер для сотрудников, кофе-пойнты.
В центральной операторной также будет располагаться и пункт управления технологическим процессом производства гексена-1 — одного из деривативов этилена.
— Основные работы на сегодняшний день — это прием сырья в печи пиролиза БА-001, БА-006 и настройка технологического режима горячей секции с дальнейшим выводом продукта на факел. Замечаний по технологическому режиму нет, — доложил начальник смены производства 7211 пиролиза и газоразделения Иван Ковалик.
Уникальная команда
Как подчеркнул директор олефинового комплекса Ленар Нагимуллин, с этого дня началась полноценная жизнь завода. Ранее комплекс по очереди тестировал и запускал основные реперные точки: «сердце» комплекса — компрессор пирогаза, компрессоры этиленпропиленового холодильного цикла, факельную систему, блок оборотного водоснабжения. Следующим этапом стал прием сырья непосредственно на печи пиролиза.
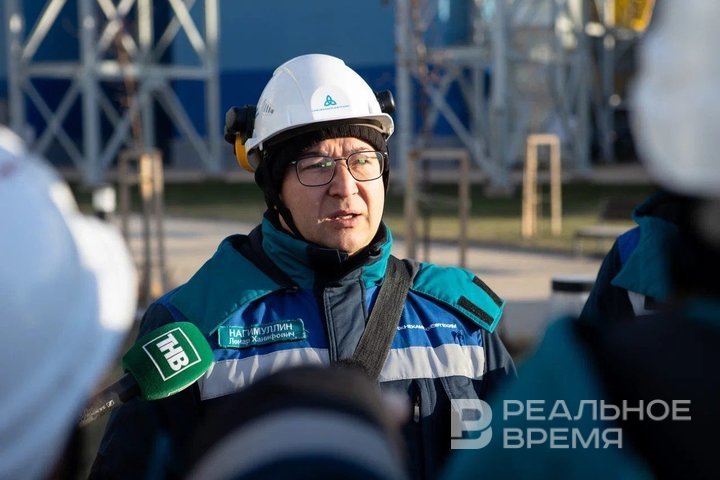
— Все объекты общезаводского хозяйства уже вошли в режим эксплуатации. Принято углеводородное сырье, осуществлен розжиг двух печей пиролиза, две — на стадии подъема температуры. На проектную мощность комплекс выйдет во втором полугодии 2025 года. С увеличением объемов продукции вырастут и налоговые отчисления, и благополучие жителей нашей республики, нашей страны, — рассказал он корреспонденту «Реального времени».
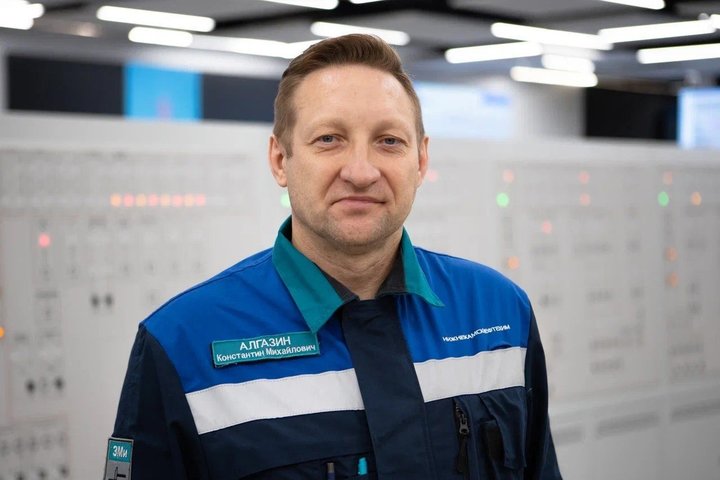
Штат комплекса полностью сформирован — на ЭП-600 работает 321 сотрудник. Все они прошли обучение и стажировку на аналогичных производствах компании. В пик пусконаладки были задействованы 750 специалистов.
— Для реализации проекта ЭП-600 мы собрали в Нижнекамске команду уникальных специалистов с опытом пуска аналогичных производств. Для усиления оперативного блока были вовлечены сотрудники «ЗапСибНефтехима», Амурского газохимического комплекса, «СИБУР — Кстово». Особенно полезным оказался опыт запуска и эксплуатации печей пиролиза, — отметил руководитель операционного блока Константин Алгазин.
С точки зрения технологий ЭП-600 является одним из самых современных и совершенных нефтегазохимических производств не только в России, но и в мире. Инвестиции в него составили около 200 млрд рублей. Уровень автоматизации и цифровизации процессов, интеграция разработанных компанией систем предиктивной аналитики, около 70 000 связанных в единую сеть датчиков — все это позволяет эксплуатировать комплекс командой в составе чуть более 320 человек. При этом обеспечен высочайший уровень контроля и снижения экологического воздействия. Объем отходов на тонну производимого ЭП-600 этилена составляет всего полтора килограмма — это в четыре раза ниже, чем у европейских аналогов, долгое время считавшихся эталоном. В общей сложности в природоохранные технологии при строительстве ЭП-600 было вложено более 5 миллиардов рублей, в том числе применены такие решения, как бездымный факел и закрытая система водоснабжения.
Вопреки санкциям
Гордятся нефтехимики и тем, что строительство этиленника не было остановлено ни на один день.
— Проекты создания производств в Западной Сибири, в Приволжском округе в предыдущие годы реализовывались при поддержке лицензиаров и вендоров. Сегодня в Нижнекамске мы впервые проходим этот этап самостоятельно. Это связано с внешними санкциями, которые ввели так называемые западные партнеры. Но мы уже научились жить в такой реальности. Во многом другие отрасли помогли — производители АСУТП, например, и производители компрессорного оборудования и не только. В целом российские машиностроители подключились. Но главное, включились все наши службы. За последние 15 лет мы не просто инвестировали более полутора триллионов рублей в создание новых мощностей, а наработали еще и уникальную внутреннюю компетенцию. В итоге сегодня нашей экспертизы достаточно, чтобы уверенно проходить пусковые операции самостоятельно. И к этому причастны не только нижнекамцы, а в том числе сотрудники «Казаньоргсинтеза», «Томскнефтехима», «ЗапСибНефтехима» и даже Амурского газохимического комплекса — мы рассчитываем, что через полтора года он также будет запускаться. Вот в этом и есть сила компании: мы объединяем усилия сотрудников всех предприятий для реализации ключевых проектов, — подчеркнул Михаил Карисалов, председатель правления и генеральный директор СИБУРа.
Компания своевременно привлекла российского проектировщика, обеспечила своевременную разработку рабочей документации и поставила оборудование на площадку. В строительстве комплекса участвовали 239 поставщиков и подрядчиков из Татарстана — это больше трети всех компаний, задействованных в проекте. Республиканские компании не только строили этиленник, но и снабжали его стройматериалами, крепежами, деталями трубопроводов, материалами для эксплуатационных нужд, оборудованием и запчастями к нему, проводили экспертизу, участвовали в проектно-изыскательских, пусконаладочных и погрузочных работах, что позволило им приобрести новые профессиональные компетенции.
— Мы завершили строительно-монтажные работы и провели полный комплекс предварительных работ, известных как «холодная» наладка. И все это без поддержки лицензиаров и вендоров — зарубежных заводов изготовителей. Мы привлекли более 20 альтернативных подрядчиков, а также сотрудников компании, которые получили большой опыт на запуске новых проектов компании, в том числе на «ЗапСибНефтехиме», — рассказал в интервью журналистам Петр Орлов, заместитель генерального директора по капитальному строительству «Нижнекамскнефтехима».
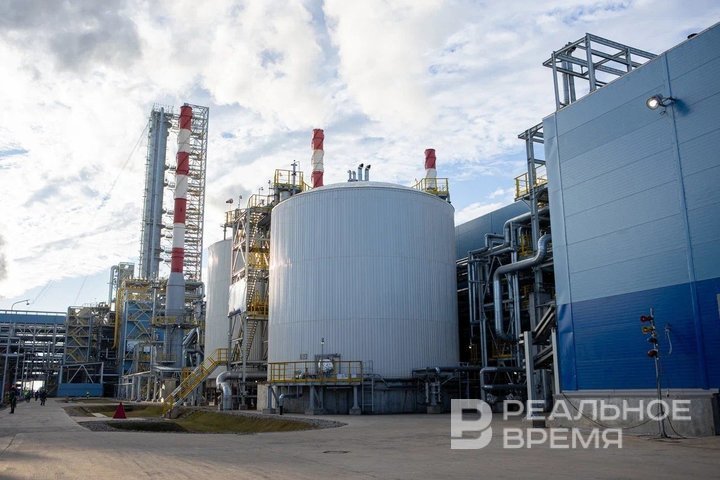
Журналистам напомнили, что ЭП-600 является частью стратегии развития химического и нефтехимического комплекса России. Запуск олефинового комплекса удвоит мощности НКНХ по олефинам (этилену, пропилену, бензолу) и даст возможность кратно увеличить выпуск продукции на других предприятиях компании. Этилен, производимый на ЭП-600, отправится на следующие переделы — производство полиэтилена низкого давления на «Казаньоргсинтезе», производство гексена, стирольной цепочки и металлоценового полиэтилена. Пропилен и бензол позволят дозагрузить имеющиеся мощности НКНХ.
— Запуск нового производства будет стимулировать развитие кластера переработки полимеров в Татарстане. Уже реализуется проект строительства гексена, появятся производство премиального металлоценового полиэтилена, установки этилбензола и стирола, а также новая установка полистирола, — подчеркнул Марат Фаляхов, генеральный директор «Нижнекамскнефтехима».
Олефиновый комплекс будет перерабатывать прямогонный бензин, поступающий от местных производителей.
— От места добычи нефти, ее переработки на НПЗ и до площадки НКНХ поставка сырья осуществляется с минимальными логистическими издержками. Все процессы будут локализованы в одном регионе и нацелены на снижение экспорта углеводородного сырья. Прием сырья на ЭП-600 — важный этап как для нашей команды, так и для всего «Нижнекамскнефтехима», в целом для развития нефтехимии республики. Здесь самое современное оборудование и технологии, уникальные кадры и бесценная практика запуска стратегически важных производств, — рассказал журналистам директор ЭП-600 Ленар Нагимуллин.
Мощность ЭП-600 по сырью составляет 1,8 млн тонн в год, или более 200 тонн в час.
— Это первый нефтегазохимический проект подобного масштаба в Татарстане со времен Советского Союза. В республике добывается значительное количество нефти. Фактически мы добавляем следующие переделы нашим партнерам, которые занимаются нефтедобычей и нефтепереработкой. Удваивая объем своего сырья, мы даем им возможность перерабатывать порядка 2 миллионов тонн нефтепродуктов практически на месте добычи, создавая продукты с высокой добавленной стоимостью, — добавил Михаил Карисалов.
Запуск производства гексена запланирован на 2025 год
В завершении пресс-тура журналистам показали строительную площадку установки по производству гексена. В качестве сырья будет применяться этилен с ЭП-600. Гексен будет использоваться для нужд компании и партнеров.
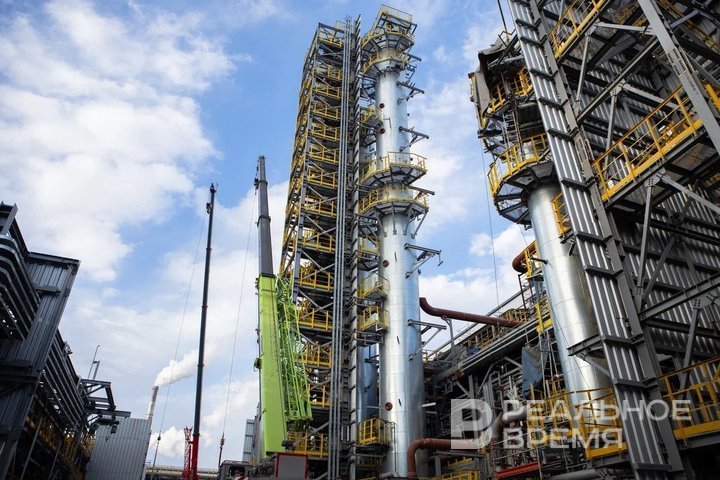
Общий прогресс проекта составляет 87%. Строительные работы завершены на 80%. Уже смонтировано технологическое оборудование, активно идет монтаж трубопроводов, начались пусконаладочные работы. На площадке трудятся 1900 сотрудников подрядных организаций. Запуск производства ожидается в 2025 году.
— Испытания на пилотной установке прошли успешно, и в 2022 году началось строительство промышленной установки мощностью 50 тысяч тонн год. После запуска производства мы полностью закроем потребность в гексене не только нашей компании, но и всего российского рынка, — подчеркнул руководитель операционного блока производства гексена Алексей Бурмистров.

Линейный гексен ранее в России не производился. Продукт, необходимый для создания полиэтилена с рядом уникальных характеристик, полностью импортировался. Технология производства гексена была разработана и запатентована силами научных центров СИБУРа — НИОСТ и «ПолиЛаба».
Импортозамещение на полную
В связке с новым этиленником нефтехимическая компания реализует целый комплекс проектов, направленных на импортозамещение широко востребованных современных синтетических материалов, в том числе полистирола, АБС-пластиков. Повышение самообеспеченности России современными синтетическими материалами создаст потенциал для дальнейшего импортозамещения конечных изделий в широком спектре отраслей, включая строительство, медицину, транспорт, сельское хозяйство и другие. Продукция нового олефинового комплекса даст возможность делать в России больше долговечных труб, надежных дорог, экологичных шин и теплоизоляционных материалов.

— Тренд на замену традиционных материалов из металла, стекла и бумаги на современные синтетические материалы не теряет актуальность. За последние годы мы вывели на рынок десятки новых марок и успешно импортозаместили большой ассортимент готовой продукции, которая ранее ввозилась в Россию. Только за отдельный 2023 год потребление полимеров в России выросло без малого на 10%. При этом все еще остается значительный потенциал для роста — почти вдвое, если сравнивать с развитыми экономиками. Есть ниши, в которых применение наших решений позволяет продлевать срок службы предметов, придавать им совершенно новые потребительские свойства. Поэтому через комплексное сотрудничество нашей науки и прикладных разработок, усилия наших инженеров и технологов, а также партнерство с клиентами будем и дальше развивать спрос, способствовать технологическому прогрессу в смежных отраслях, — рассказал Михаил Карисалов.
По данным исследования Высшей школы экономики, с учетом всей длины цепочки производств конечных изделий из современных синтетических материалов СИБУР поддерживает в общей сложности более 700 тысяч рабочих мест в российской экономике. Совокупный объем инвестиций компании в строительство и модернизацию нефтегазохимических мощностей за предыдущие 15 лет превысил 1,5 триллиона рублей, в том числе в Волжском кластере — 0,6 трлн рублей. С учетом других географий в инвестиционном портфеле компании находятся проекты более чем на 1,7 трлн руб. с горизонтом ввода в эксплуатацию в 2027-2028 годах. В настоящее время более половины EBITDA компании обеспечивается работой производств, запущенных около 10 лет назад и менее.
Подписывайтесь на телеграм-канал, группу «ВКонтакте» и страницу в «Одноклассниках» «Реального времени». Ежедневные видео на Rutube, «Дзене» и Youtube.