На ТАИФ-НК завершается остановочный ремонт
Более 500 привлеченных специалистов и тысячи собственных сотрудников за три недели привели в порядок основные производства нефтеперерабатывающего комплекса «ТАИФ-НК»

Три завода. Более тысячи единиц оборудования. На то, чтобы вскрыть, получить экспертную оценку и полностью подготовить все огромное хозяйство АО «ТАИФ-НК» к безаварийной работе в следующий межремонтный период, отводится всего 20 дней. Работа кипит и днем, и ночью. Сейчас остановочный капитальный ремонт на нефтеперерабатывающем комплексе «ТАИФ-НК» уже почти завершен. За тем, как ставятся последние штрихи, наблюдал журналист «Реального времени».
Привлечены 5 экспертных организаций
Понять, в каком состоянии оборудование, оценить уровень износа и характер ремонтно-восстановительных работ или и вовсе необходимость замены целых узлов уже сейчас или на следующий год при точно таком же остановочном капремонт, — задача экспертов.
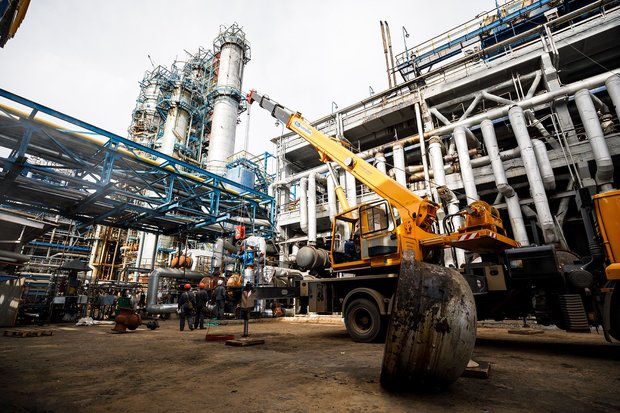
— У нас работает порядка 5 экспертных организаций с разных регионов. Из Казани, Уфы, Москвы… Специалисты очень высокого уровня. В процессе запланированных работ по экспертизе промышленной безопасности и определения остаточного ресурса, проведения технических обследований ими выявляются отклонения и дефекты, которые оперативно устраняются, — пояснил журналисту главный механик АО «ТАИФ-НК» Рустам Багавиев.
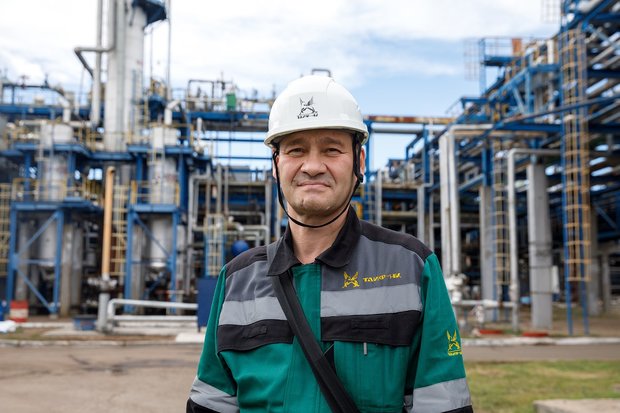
Представителя одной из экспертных организаций — инженера-дефектоскописта казанского Инженерного центра по экспертизе и диагностике Рустама Зарипова журналист «Реального времени» застал за обследованием многотонных емкостей на Нефтеперерабатывающем заводе.
— С ТАИФ-НК сотрудничаем уже больше 10 лет. Каждый год мы участвуем в экспертизе промышленной безопасности. Наша задача — обследовать оборудование, найти дефекты и передать информацию руководству производства. И они уже устраняют. Если дефекты выявлены, они оперативно устраняются. От нашей организации сейчас здесь работают 7 человек. 2 эксперта, а остальные — дефектоскописты, — пояснил Рустам Зарипов.
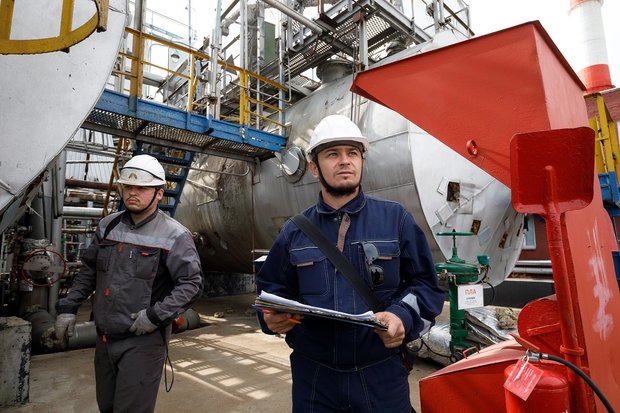
Масштабы работы в такие сжатые сроки — поражают: в установленном порядке производства останавливают. И с этого момента включается «таймер обратного отсчета».
— В рамках трех заводов мы вскрываем порядка 1000 единиц технологического оборудования. Вскрыть, почистить, заменить часть устройств, отремонтировать — это действительно достаточно масштабные работы. Они проходят с привлечением подрядных организаций, количество специалистов которых доходит до 500 человек, — отметил главный механик АО «ТАИФ-НК» Рустам Багавиев.
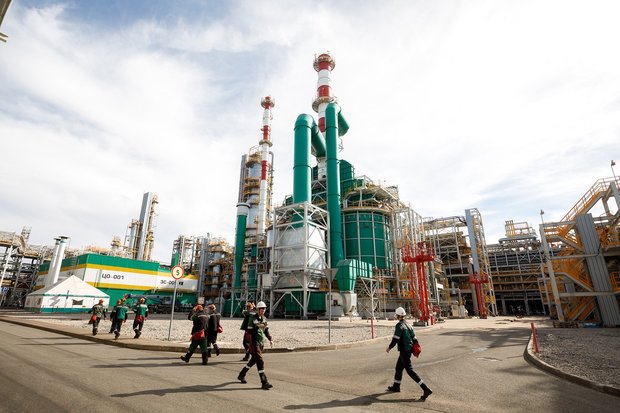
Параллельно собирается информация по уровню износа оборудования и идет наработка задач на следующий капитальный ремонт. В межремонтный период формируются заявки и определяется перечень будущих подрядчиков под конкретные задачи уже на следующий капремонт. Делать это нужно заблаговременно.
— Есть такой момент, что сентябрь — самый активный в этом плане период: пора капремонтов. Очень большое количество подрядчиков привлекается одномоментно на различные производства. И в этом есть определенные сложности. Но мы используем и возможности электронно-торговой площадки, приглашаем на участие в торгах участников, которые к нам заявляются письмами. Кроме того, когда мы заинтересованы в каком-то подрядчике, мы едем с ним по месту, знакомимся с их оборудованием, количеством персонала… То есть определяем для себя на будущее: может ли данная организация справиться с теми задачами, которые ей могут быть поручены в рамках договора, — рассказал главный механик АО «ТАИФ-НК».
На НПЗ в период капремонта не останавливали только очистные
— Мы уже закончили практически. Остатки добиваем. Капремонт всегда охватывает полную разборку, ремонт и чистку практически всего оборудования основной технологической площадки. Это 1, 2, 3-й и 5-й цеха. Плюс выборочно резервуары 8-го цеха, согласно графику ремонта. Плюс резервуары 7-го цеха. В работе остается только 9-й цех, где капремонта нет, там делается все на ходу. Это очистные. Все остальное оборудование — колонны, емкости, теплообменники — все вскрывается, ремонтируется, чистится, осматривается экспертами и собирается, — в интервью журналисту «Реального времени» сообщил директор Нефтеперерабатывающего завода АО «ТАИФ-НК» Владимир Лахомов.
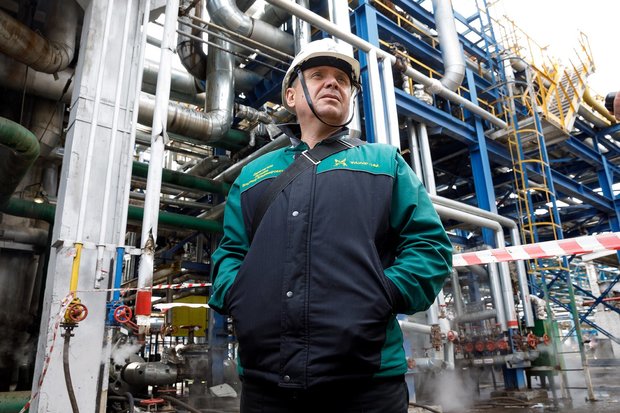
На настоящий момент остались, можно сказать, небольшие дошлифовки и большая уборка. После того как капремонт завершается, предстоит вывезти довольно много «мусора». Точнее — вторсырья. Например, на одной из колонн первого производства НПЗ (перегонка нефти) поменяли насадку, отвечающую за разделение нефти на целевые фракции.
— Сейчас колонну К-10 уже закрыли. Меняли насадку — ту самую часть, где происходят массообменные процессы. Если в других колоннах — «тарелки», то здесь — насадка: пакетированная сетка. Жидкость падает вниз, пар летит наверх. Замена насадки производится по состоянию. Сейчас мы заменили вторую насадку, внесенную в план капремонта в прошлом году. В межремонтный период заказали и приобрели насадку, сейчас — поменяли. В следующем году будем менять третью насадку, — пояснил директор НПЗ.

Остатки сетки отправятся по договору предприятия со специализированной организацией — на вторсырье. Туда же поедут отработавшие положенный срок секции теплообменников аппаратов воздушного охлаждения и замененные на новые элементы части общей системы для масляного и антифризного компрессоров, устаревшая арматура и другое железо.
Параллельно с основными работами по капремонту происходит оценка возможностей импортозамещения в ремонте, восстановлении и замене оборудования. Вопрос насущный для отечественных предприятий во всех отраслях.

— В этом году промышленность оказалась в непростых условиях: очень много импортного оборудования, а оригинальные запчасти — никто не привез. Иностранные компании из недружественных нам стран отказали в поставках. Причем даже тех деталей, которые уже были изготовлены и были готовы к отгрузке. Соответственно, идет проработка с российскими производителями. Один из выходов в том, что мы деталь, которую нам не привезли, но которую требуется заменить, везем — эскизируем на 3D-сканере. У нас это можно сделать тут рядом — в соседней организации. Они делают по 3D-сканеру чертеж, потом по этому чертежу можно изготовить деталь и установить ее в оборудование. Кроме того, не все оборудование — железное. Часть его — сальники, резинки, манжеты — в России есть кому изготавливать. Знакомимся, встречаемся, рисуем, разговариваем. Работа — ведется, ситуация — под контролем, — успокоил журналиста Владимир Лахомов.

Есть более важные и непростые вопросы. Например, подбор тех же подрядчиков на исполнение экспертных и ремонтных работ по заказу «ТАИФ-НК».
— Попасть к нам в качестве подрядчика на выполнение работ — самое сложное. Желающие есть, и их немало. Но все-таки производство у нас первой категории опасности и абы кого даже на обычные работы сюда заводить нельзя. Территория за двумя заборами — это о многом говорит. Перед тем как заключать договор, подрядчиков очень активно проверяет наша служба безопасности, — пояснил директор Нефтеперерабатывающего завода Владимир Лахомов.
Одни из тех, кто прошел сквозь частое сито проверки, — специалисты Центра пожарно-технической безопасности из Альметьевска. Услуги, что предлагает компания — довольно специфические: чистка огромных резервуаров, предназначенных под сырье.

— Нефтяные резервуары — огромные — 67 метров в диаметре, объем — 50 тыс. кубов. За год все самое тяжелое опускается на дно и там собирается. Раньше резервуары чистились людьми: человек в противогазе с лопатой заходил в резервуар, а на выходе его ждут другие люди — с тачками. Так и убирали тяжелые осадки. Примитивно все было. Или откачивалось насосами. Сейчас это делает машина — робот, который ездит с помощью гидравлики внутри резервуара. Он вооружен насосом, которым собирает все со дна — воду, парафиновые отложения, механические примеси, — рассказал Владимир Лахомов.
Собранные примеси и осадки перекачиваются в соседние резервуары и в дальнейшем также идут на переработку.
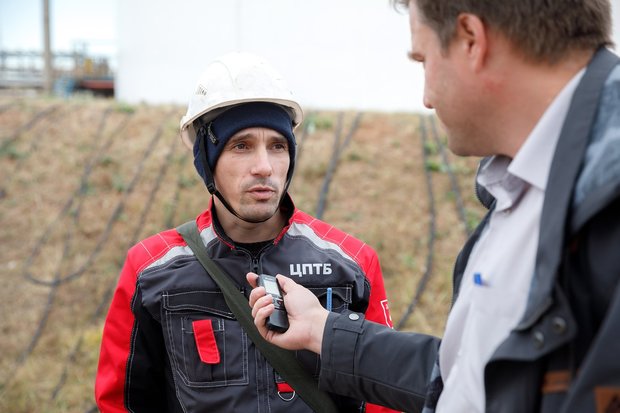
— Робота мы вообще создавали для того, чтобы производить работы в замкнутом пространстве — для очистки РВСов. Занимаемся этой работой уже давно. И разработки ведутся — уже давно. Сейчас образцы пошли в серийное производство. Задачи и условия бывают разные: наши роботы работают и у нефтяников, и в Казахстане, и в северных регионах, и у нас — в Татарстане. И под каждую мы можем создать своего робота. Здесь, например, работал робот, созданный именно под очистку резервуара емкостью 50 тыс. куб. метров, — пояснил мастер подрядной организации Павел Ряхов. По словам специалиста, его компания выполняет заказы «ТАИФ-НК» уже второй год и намерена развивать сотрудничество.
Первый полномасштабный остановочный
Комплекс глубокой переработки тяжелых остатков пиролиза нефти капремонт проводит уже не впервые. Еще в режиме опробования, а затем — опытно-промышленной эксплуатации оборудование приходилось останавливать, вскрывать, проверять, донастраивать, менять — как-никак и технология достаточно нова, и среды, с которыми приходится работать, — агрессивны, и технология требовала шлифовки в реальных условиях. Потому то, что было раньше, именно полномасштабным капремонтом назвать нельзя. Сейчас дело иное.
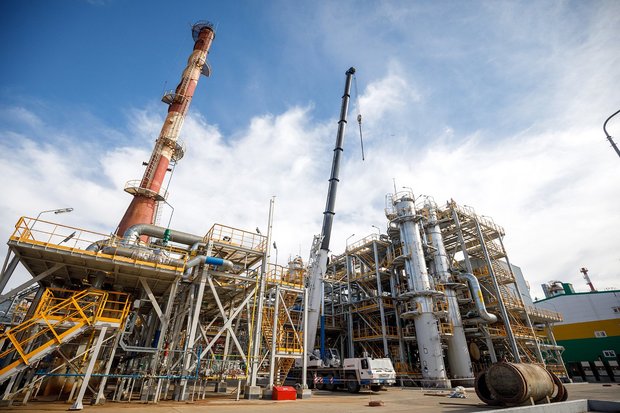
— У нас, действительно, первый такой ремонт, когда мы планово останавливаемся после долгой работы. Соответственно, привлечено большое количество экспертов, которые ревизируют все оборудование. Как в рамках государственного контроля, так и в рамках собственного дополнительного обследования, — пояснил главный инженер КГПТО Артур Уразайкин.
В целом характер проводимых работ мало чем отличается от тех, что в это же время ведутся на других производствах нефтеперерабатывающего комплекса: ревизия теплообменного оборудования, динамического оборудования, оценка состояния и уровня износа. Но есть и разница, причем существенная.
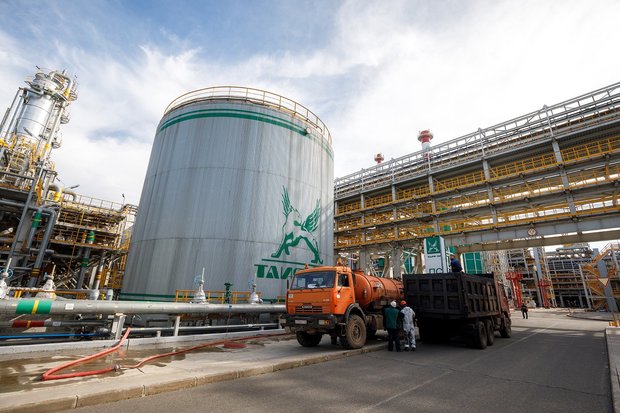
— Уникальна сама технология, по которой здесь происходят производственные процессы. Уникальны те среды, которые в процессе производства возникают и которые обращаются в оборудовании и в аппаратах, соответственно, уникальны и подходы, которые требуются при обследовании. Это должна быть всеобъемлющая, всесторонняя и при этом неразрушающая ревизия всего оборудования. Так как технология новая, то и для экспертов многое в новинку. Приходится придумывать какие-то новые подходы в своей работе, в зависимости от тех задач, которые мы перед ними ставим. Мы сами закупили довольно много уникального оборудования, позволяющего изучать внутренние поверхности аппаратов объемно, чтобы точно видеть — что и как обстоит с оборудованием, которое прошло определенный период эксплуатации. Такое оборудование редко используется в нашей отрасли. Используются изотопные приборы, которые находятся под контролем Росатома. Фактически, речь идет о рентгене для оборудования, который позволяет видеть, что, собственно говоря, внутри происходит. Обычные приборы измерения уровня на наших средах не работают, — рассказал Артур Уразайкин журналисту «Реального времени».

Основной реакторный блок VCC в момент приезда группы «Реального времени» также был остановлен на капремонт. Это происходит раз в два года — на чистку оборудования и точечный ремонт внутренней защитной поверхности. Здесь без человеческих глаз и рук — просто не обойтись.
— В этих аппаратах сейчас работают специально подготовленные люди в скафандрах с большим забралом, по бронированным шлангам подается воздух. Опускается сверху до самого низа в эти 3 аппарата, буквально по сантиметру обследуют всю внутреннюю поверхность, где это необходимо, — проводят чистку, ремонтные работы проводят. Это сердце наших процессов и мы за его состоянием внимательно следим, — сообщил главный инженер производства.
Один из главных результатов почти годовой работы КГПТО с серьезной загрузкой, помимо выросшего до более чем 90% выхода высококачественных светлых нефтепродуктов из каждой тонны нефтяного сырья и увеличения производств продукции «ТАИФ-НК» в целом, еще и проверка всех тех новаций, что были реализованы при строительстве комплекса.
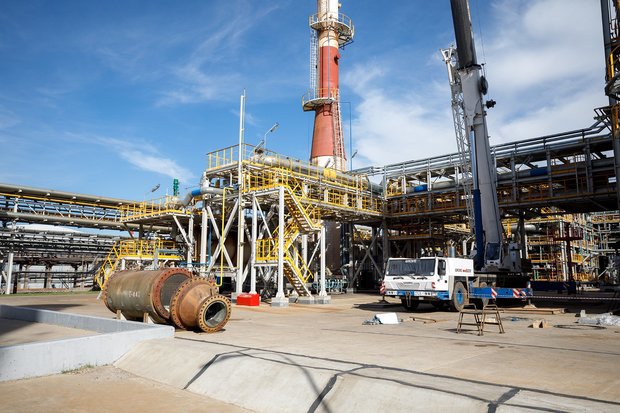
— За этот период у нас накопилось досье на каждый агрегат и те точки, на которые мы прогнозируем в будущем проблемы, и мы на эти точки обращаем особое внимание. Мы не жалеем времени и ресурсов на то, чтобы быть уверенными в том, что следующий год отработаем на тех же нагрузках и без остановок. Все, что мы сегодня вкладываем в экспертизу, в обследования, это инвестиции в безаварийную работу в будущем. Были узлы и аппараты, к которым у нас были вопросы. Мы технические решения применили и сейчас, вскрывая оборудование, мы видим, что практически все сложные моменты — исключены, либо нивелированы полностью, — с нескрываемой гордостью поделился Артур Уразайкин.
Капремонт начался с закрытой пропарки
Провожатым группы «Реального времени» по территории завода бензинов «ТАИФ-НК» стал главный механик производства Андрей Миненков. По его словам, перед тем, как приступить к обследованию оборудования, емкости полностью освободили от сырья и полупродуктов. Это обязательная часть процедуры для любого нефтеперерабатывающего производства.
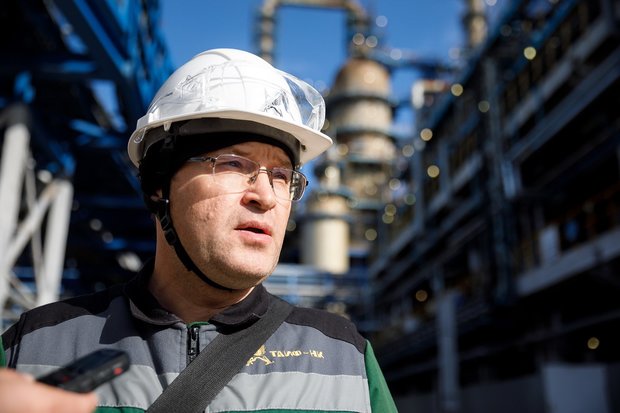
— Начали с закрытой пропарки с использованием специальных реагентов. В пар во время этой процедуры подаются специальные химреагенты, которые убирают запах, снижают до минимума воздействие как на окружающую среду, так и на человека. Добавки полностью купируют любые вредные испарения, — сообщил Андрей Миненков.
Как и на других производствах комплекса, на заводе Бензинов эксперты провели тщательную толщинометрию трубопроводов и оборудования. Всего в ходе капремонта-2022 экспертизу промбезопасности и техническое диагностирование прошли более 200 единиц оборудования. Часть подвергнута не только ремонту, но и некоторому усовершенствованию.
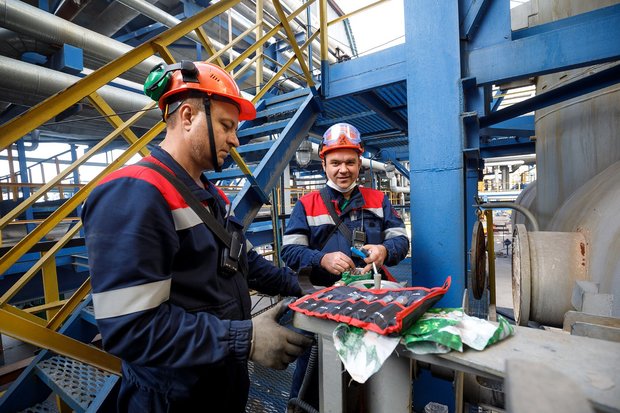
— По проекту московской организации «Автотехпроект» в этом году на регенераторе выполнили очередной этап замены футеровки на более современную. Футеровка — это слой специализированного бетона, предотвращающий воздействие агрессивной среды на металлический корпус аппарата. Была проведена работа по демонтажу старого слоя футеровки, панцирной сетки, с последующей подготовкой поверхности, приваркой анкеров и нанесением футеровочной смеси. Данная футеровка позволит сократить количество ремонтов в процессе эксплуатации, — пояснил главный механик завода бензинов журналисту. И добавил, что однослойная защита уже имеется на части оборудования, причем показала себя гораздо более надежной, чем многослойная. Кроме того, у нее в разы выше ремонтопригодность.
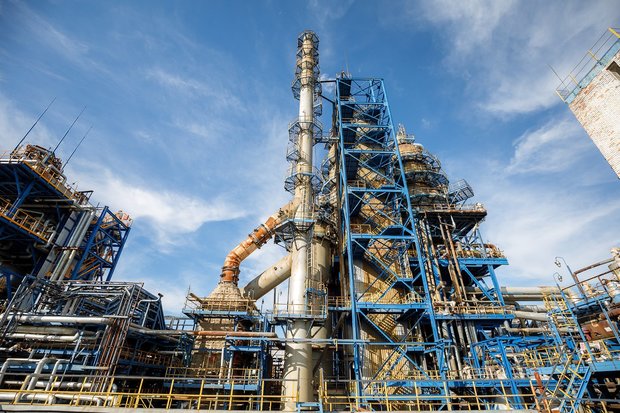
Также в ходе ремонта была проведена замена экономайзера котла-утилизатора. Старый скоро отправится на вторсырье, а новый после покрытия слоем изоляции будет готов к запуску. Для того, чтобы демонтировать отработавшее свое оборудование и установить на место новое, пришлось заказывать специальный — 400-тонный кран.
Чуть меньший по грузоподъемности, но тоже внушающий уважение кран расположился перед рядом колонного оборудования.
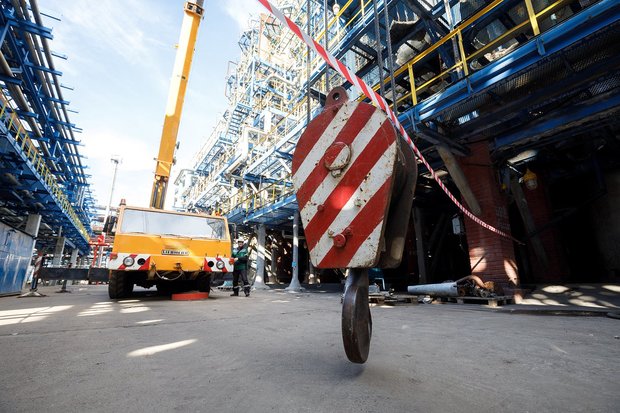
— За этим оборудованием располагается площадка, на которой необходимо установить прошедшие ревизию предохранительные клапаны. Они довольно тяжелые, а расположение оборудования таково, что сделать это можно только с помощью специальной техники и только с определенных точек. Причем справиться с этим сможет не каждый кран, — рассказал о происходящем Андрей Миненков.
Ведется работа по проверке всех систем, проводится опрессовка уже отремонтированного оборудования, выполняется ремонт изоляции. Завершаются работы по замене градирни. Параллельно решается комплекс задач по импортозамещению.
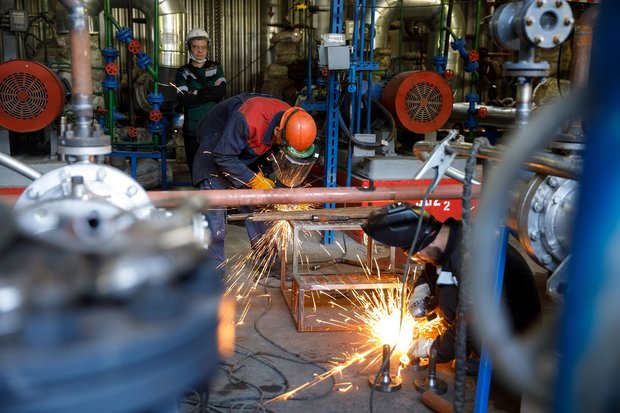
— В данный момент у нас ведется большая работа по подготовке компрессора производства «Сименс» к его модернизации. Работает подрядная организация, проводит необходимые замеры и исчисления, и уже на будущий год будет проведена работа по модернизации — замене проточной части и других элементов на российское производство. Также проводятся мероприятия по снятию замеров, определению состава уплотнений насосно-компрессорного оборудования, которые впоследствии будут изготавливать в рамках импортозамещения, — отметил главный механик завода бензинов.
Сейчас ведутся активные переговоры с возможными российскими исполнителями и других заказов на изготовление деталей, узлов и оборудования для нужд завода бензинов АО «ТАИФ-НК».
Главные механики производств России объединились
Вопрос импортозамещения сегодня довольно остро стоит перед подавляющим большинством российских производств. Об этом журналисту «Реального времени» сообщил главный механик АО «ТАИФ-НК» Рустам Багавиев. Решением проблемы главные механики предприятий страны решили заниматься сообща.

— У нас организован научно-технический центр при Совете главных механиков, где главные механики ведущих производств России сообща ведут работу по формированию общей базы исполнителей услуг, изготовителей материалов, деталей, запчастей и т.д. для импортного оборудования. Мы создали также и свою базу по возможным компаниям-исполнителям. В рамках этой работы мы инспектируем организации, знакомимся с персоналом, оборудованием, наличием лабораторий, конструкторских отделов, технического контроля. И после каждой такой поездки инспекции нашими специалистами создается отчет, с описанием того, что мы увидели, перечня услуг, которые они нам могут предоставить. Позже — при выборе подрядных организаций, мы используем эту базу, — поделился Рустам Багавиев.
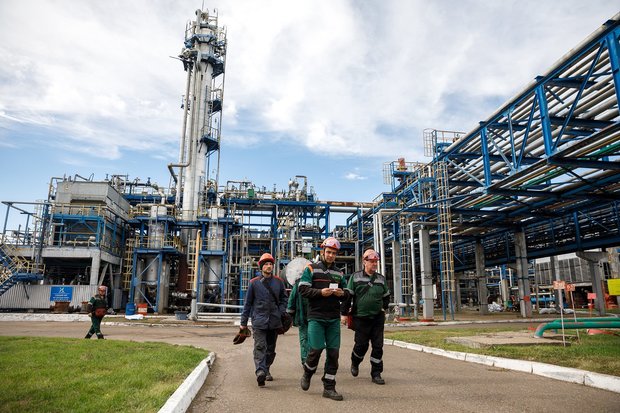
Он также особо подчеркнул, что, насколько бы сложные задачи не стояли перед персоналом АО «ТАИФ-НК» и привлеченными комплексом подрядными организациями, сроки, отведенные на капремонт, — выдерживаются строго. Пуск производств будет произведен точно по графику.
Подписывайтесь на телеграм-канал, группу «ВКонтакте» и страницу в «Одноклассниках» «Реального времени». Ежедневные видео на Rutube, «Дзене» и Youtube.