Мощнее и экологичнее: КОС подвел итоги остановочного ремонта
Во время пресс-тура журналистам рассказали о результатах модернизации предприятия

Дроны, ультразвук, 3D-сканирование — это не кадры фэнтези, а современные реалии «Казаньоргсинтеза». Предприятие впервые во время остановочного ремонта массово использовало цифровые инструменты. Впечатляют и результаты модернизации: повысилась производительность завода поликарбонатов, на заводе по производству и переработке полиэтилена низкого давления (ПППНД) заработала установка рекуперации сбросных газов, которая позволяет возвращать часть неиспользуемых газов в производство вместо сжигания их на факельной установке, что, в свою очередь, снижает нагрузку на атмосферу. Подробнее — в материале «Реального времени».
Ремонт с опережением графика
Казанское предприятие СИБУРа завершило плановый осенний остановочный ремонт. В этом году он проходил в новых реалиях. Впервые массово использовались цифровые инструменты, позволяющие безопасно провести работы повышенной опасности и обследование технологического оборудования. На этапе опрессовки для нахождения утечек применялся ультразвуковой течеискатель. В ходе проверки мест производства работ повышенной опасности и обследования факелов использовался дрон-сервис. Также в рамках реализации программы по технологической защищенности сделано 3D-сканирование узлов и деталей компрессоров (реверс-инжиниринг). В перспективе эта инициатива позволит подготовиться к замене недоступных запасных частей в ходе будущих ремонтов.
Заводы на ремонт останавливались поэтапно. Первый этап был завершен в первой декаде октября, второй — в первой декаде ноября. Работы были выполнены с опережением графика. Как рассказали на предприятии, сокращения остановочного периода удалось достичь за счет оптимизации внутренних процессов.
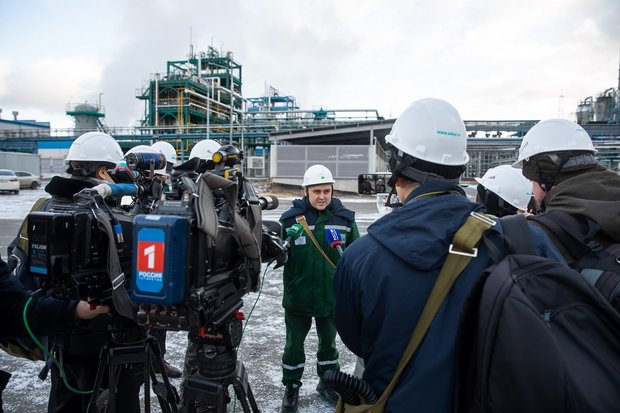
— В этом году в остановочный ремонт мы зашли с амбициозными планами. Изначально поставили себе задачу — сократить период ремонта на 4 суток. Эта цифра была взята не просто так. Мы изучили опыт наших коллег с других предприятий СИБУРа. Совместно с ними провели мозговые штурмы, определили работы критического пути и составили четкие графики. По некоторым позициям даже почасовые графики. Все эти подготовительные работы позволили нам провести все в намеченные сроки. Более того, по некоторым производственным цепочкам мы запустились раньше на сутки, где-то даже на двое от запланированных нами сроков, — добавил главный инженер «Казаньоргсинтеза» Рустем Музафаров.
Вторичная переработка сбросных газов
В рамках остановочного ремонта кроме традиционных работ по профилактической чистке оборудования, замене деталей и узлов были реализованы проекты по модернизации. Один из них — запуск установки рекуперации сбросных газов на заводе ПППНД. Она предназначена для сбора и возврата обратно в процесс тех газов, которые раньше сбрасывались на факельные установки для сжигания.
Установка строилась на КОСе в течение двух лет. После остановочного ремонта она уже начала работать в полную мощность. Как рассказал журналистам ведущий инженер-технолог производства полиэтилена низкого давления Артур Аглямзянов, предприятие не собирается останавливаться на достигнутом в области экологической безопасности, на подходе новые проекты.
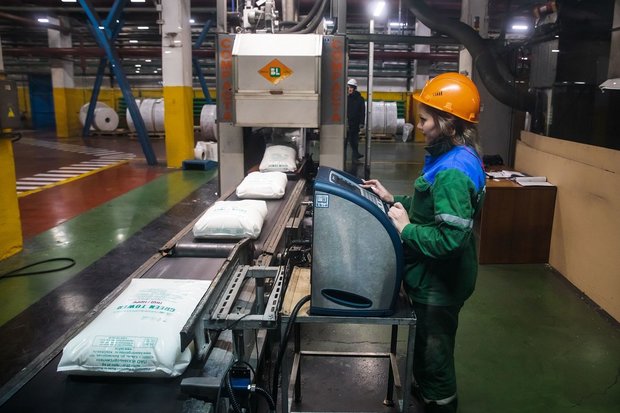
— Сейчас у нас готовится большой инвестпроект по установке мембранных фильтров, благодаря которым мы сможем собирать сбросы этилена на факел. Они и сейчас незначительные, менее 10%. А в будущем их не будет вообще, так как благодаря этим фильтрам мы сможем их возвращать обратно в процесс производства этилена, — уточнил он.
Видимо, не за горами тот момент, когда завод ПППНД полностью избавится от сбросов на факел, все будет возвращаться обратно в производство.
Модернизация завода поликарбонатов
Еще один амбициозный проект реализовали на заводе поликарбонатов, здесь произвели замену полимерного насоса. Новый насос изготовлен в Японии. На предприятии не скрывают, что в текущей геополитической ситуации транспортировка насоса и его комплектующих стоила больших трудов.
— Все лето мы занимались тем, чтобы привезти этот насос из Японии в нашу страну. В итоге он со всеми комплектующими, а это довольно большая поставка — 47 тонн, — был перевезен. Сначала по воде, через пролив между Владивостоком и Японией, а далее специальным самолетом до нас. Успели прямо к началу остановочного ремонта, — рассказывает главный инженер завода поликарбонатов Ринат Закиров.
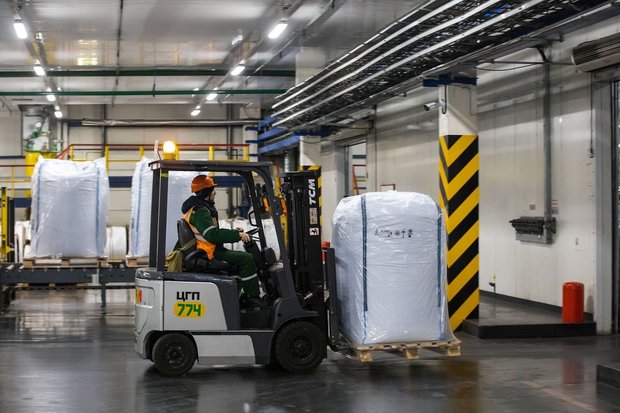
А вот к процессу установки химики подошли с креативом.
— Необходимо было демонтировать старый насос и его фундамент, залить новый, смонтировать оборудование. На все это было буквально 23 дня, поэтому использовали инновационные технологии, так называемую смолизацию. Для этого еще во время подготовки вокруг насоса был укреплен грунт, чтобы не ломать полностью существующий фундамент, а использовать его часть, смонтировав новый поверх него. Старый фундамент тоже ломался нетрадиционным способом — кувалдой и отбойным молотком. Была нанята подрядная организация, которая срезала фундамент с помощью специального оборудования, — поделился подробностями Ринат Закиров.
Все успели сделать вовремя, даже с опережением на полторы сутки.
Пять из шести факелов работают в бездымном режиме
Для повышения экологичности производства в рамках остановочного ремонта была проведена работа по переводу одного из шести факелов с пара на воздух. Прогресс по данному объекту составил 80%, модернизацию планируется завершить в первом квартале следующего года. Эта технология позволяет избежать образования излишнего количества сажи при горении, а значит, снизить нагрузку на атмосферу. Напомним, ранее по такой схеме были модернизированы уже четыре факела. Работы по переводу последнего, шестого факела планируют начать в 2023 году.
В остановочном ремонте были задействованы более 2 тыс. сотрудников. Четверть из них — персонал подрядных организаций. Также для обучения работников «Казаньоргсинтеза» использованию нового оборудования активно привлекались сотрудники других предприятий компании СИБУР.
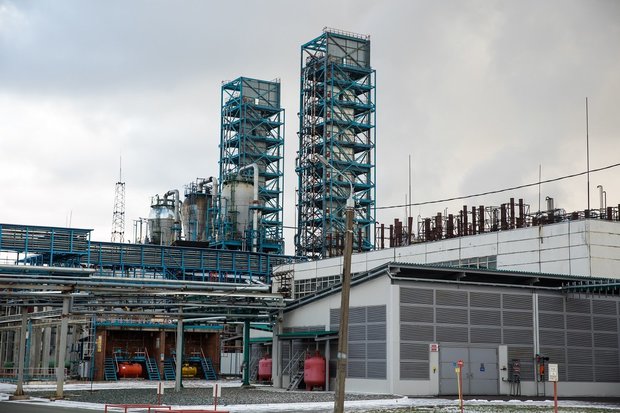
С 2023 года предполагается перевод заводов по производству поликарбоната и по производству бисфенола А на увеличенный межремонтный интервал. Например, раз в два года. Подготовка к переводу была проведена уже в этот остановочный ремонт.
— Такой перевод позволит сократить количество плановых остановок и повысить эффективность производства продукции. Снижение числа остановок, в свою очередь, ведет к уменьшению нагрузки на окружающую среду, так как максимальное воздействие происходит именно в период останова и запуска производства, — объяснили на предприятии.
Подписывайтесь на телеграм-канал, группу «ВКонтакте» и страницу в «Одноклассниках» «Реального времени». Ежедневные видео на Rutube, «Дзене» и Youtube.